This post has already been read 4920 times!
Reconsidering your pallet wrapping options in the light of new materials and technologies
Pallet wrapping is one of the most foundational processes in logistics, but as demand picks up, it’s worth a review. Warehouses today face more pressure than ever to ship goods safely, quickly and often with fewer workers. In light of these rising standards, businesses should consider if they’re using the best pallet wrapping techniques.
This could better protect your product, save on damages, ensure customer satisfaction, and ease manual workload… | A Guide to choosing the Best Pallet Wrapping For Your Needs Share on XAs with many things, the best wrapping method depends on the warehouse and even the specific shipment at hand. Here is a rundown of the most common approaches and when they might be the best option.
Pallet Wrapping Techniques by Approach
There are a few ways to divide pallet wrapping techniques. The first and most straightforward is by the actual workflow, whether it’s manual or automated.
Manual Pallet Wrapping
Manual wrapping — also called hand wrapping — is the most straightforward approach. While these approaches have fallen out of favor in many circles, they can still provide some advantages. Humans are more flexible than machines, so if a pallet has an unusual shape or size or requires more delicacy, hand wrapping may be ideal.
On the other hand, 73% of employers today cite difficulty finding enough staff. Consequently, some facilities may not have enough employment levels to maintain peak productivity while manually wrapping pallets.
Generally speaking, manual wrapping is sufficient for smaller operations or those with many unusual pallet loads. However, in most cases, automation is the better option.
Machine Pallet Wrapping
Machine wrapping comes in many forms, but they all share a significant advantage — they’re far faster than manual methods. Because they don’t require as many employees, these machines also help mitigate labor shortages. While they don’t perform as well with unusually sized or shaped loads, they offer more precision with standardized pallets.
Automated wrapping machines generate data as they work, leading to ongoing improvements. This technology helps validate load wrapping performance by revealing trends over where errors arise, which warehouses can use to adjust the process.
The most considerable downside to machine wrapping is its high upfront costs. The efficiency savings will compensate for that over time, but the return on investment may be too slow for smaller operations to justify it.
Pallet Wrapping Techniques by Material
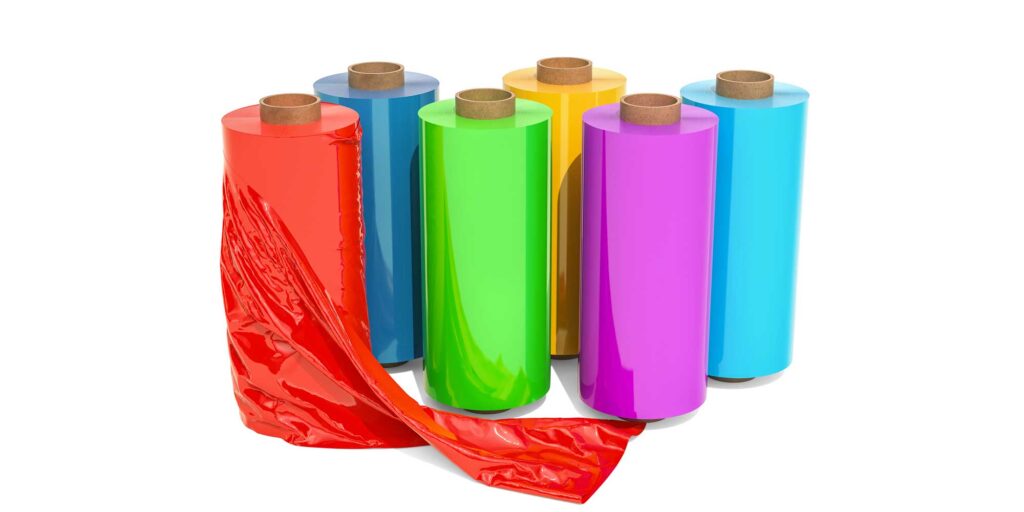
Another way to divide pallet wrapping techniques is by the material they use. There are more wrapping materials on the market today than many businesses may realize, each with unique strengths and weaknesses. Here are a few of the most notable.
Cast Film
The unofficial industry standard for pallet wrapping is cast film. This material — mostly made from linear low-density polyethylene (LLDPE) — offers uniform thickness throughout the roll, quiet unrolling and high clarity, which is helpful for barcode scanners. Its quick production process also means it’s typically inexpensive, which is particularly helpful amid rising industrial rents and other high expenses.
What are the best materials and techniques for pallet wrapping? It depends on your goods and shipments. Here's a Guide to Choosing the Best Pallet Wrapping For Your Needs Share on XCast film is technically less stretchable than blown film — the other major category — but it requires less force to stretch. Consequently, it’s often the stretchier material in practice. However, it has lower stretch memory, making it less durable. Wrapping in several layers can help account for that loss, but that incurs higher material costs.
Blown Film
The other of the two largest groups of pallet wrapping materials is blown film. As the name implies, this wrap comes from a process that blows hot resin to stretch and cool it. While the process takes longer and costs more, it gives blown film some unique advantages.
Blown film is more tear and puncture-resistant than cast film. It also clings better and produces less waste in manufacturing, making it a leaner material. However, it’s also more expensive and difficult to apply. Many facilities also note it’s much louder when unrolling, which can disrupt the workplace.
Engineered Cast Film
As the most popular pallet wrapping technique, cast film is a broad category covering several unique subtypes with specific advantages and disadvantages. One of the most important of these is engineered cast film. Engineered film uses far more layers than standard cast wrap, increasing its strength, even at lower gauges.
Engineered film uses a blend of high-performance materials that conventional wraps may not offer. As a result, it stands up better to tears and punctures and clings to material better. Considering as much as 11% of some loads arrive at distribution centers damaged, that advantage is hard to ignore. However, it’s less widely available and may come at a higher cost, making it less accessible for smaller operations.
Pre-Stretched Film
Another essential type of cast film to know is pre-stretched film. As its name implies, manufacturers stretch this material before wrapping it around the roll. This pre-stretching makes it far easier to handle, which can help reduce material consumption and save costs.
Because workers don’t have to pull as hard to apply pre-stretched film, it can prevent overexertion injuries. Workplace injuries cost employers $163.9 billion in 2020, so this accident prevention carries cost benefits, too. The only major downside to pre-stretched film is it’s only suitable for manual wrapping techniques, so automated processes can’t capitalize on it.
Paper Wraps
While LLDPE and similar materials are the most common wrapping materials, some promising alternatives have emerged recently. Paper wraps use flexible, durable paper to keep pallet loads in place while minimizing companies’ plastic consumption. This provides more strength and durability than conventional alternatives.
Paper wraps also shield shipments from sunlight, which is vital for some more sensitive products. Some vendors may also cite environmental benefits given their recyclability, but businesses should analyze these claims carefully. Paper requires extensive energy to produce and contributes to deforestation. As strategies like closed-loop supply chains become more popular, companies must be careful to avoid “greenwashing” — or claiming to be more sustainable than they are.
Choosing the Best Pallet Wrapping Techniques
Given each material and process’s unique characteristics, there’s no one answer to the best pallet wrapping techniques. That varies depending on the specific operation at hand.
Generally speaking, machine wrapping is preferable to manual wrapping, as it’s far faster and more affordable long term. With freight demand expected to grow by 40% by 2045, that efficiency will become increasingly important. Even lower-volume facilities should consider automation amid this trend, starting by automating a single process before slowly increasing it to offset upfront costs.
Machine wrapping is generally preferable to manual wrapping. It's faster and more economical in the long term. | A Guide to choosing the Best Pallet Wrapping For Your Needs Share on XConsidering this rising demand, high-volume facilities should also consider low-cost, easy-to-implement wrapping materials. Engineered cast film is often one of the best choices, though standard cast film may be sufficient if engineered wrap is too expensive. Contrastingly, blown film may be best for low-volume but high-value shipments, given its reliability.
Companies with unique needs should consider unorthodox alternatives like paper wraps. These may come with higher upfront costs but can provide valuable benefits that other solutions don’t, like protection from sunlight.
Find the Best Technique for Your Business
Finding the best pallet wrapping techniques means understanding what’s available and what different shipments need. When you know your budget, all available options and goals, you can make a more informed decision.
Are you using the most suitable wrapping materials and processes to optimize your operations?
Recommended Posts
- Are Micro Fulfillment Centers the Next Frontier in Retail Logistics?
- Rethinking Defense Supply Chains with Network-Based Command Centers
- How to Use Predictive Analytics to Streamline Cross-Border Logistics
- AI Plus Humans for Resilient Freight Forwarding in a Complex World
- Modern Defense Supply Chains: The Essential Capabilities for Multi-Domain Operations
- 6 Ways Technology Makes the Supply Chain More Efficient - October 25, 2023
- How Digitization is Enhancing Supplier Relationship Management - May 9, 2023
- A Guide to choosing the Best Pallet Wrapping For Your Needs - November 28, 2022