This post has already been read 15550 times!
Automation is often one of the best tools businesses have for streamlining packaging and is considerable advantage in the current tight labor market. As companies face rising demand and growing expectations — like the one- or two-day shipping most customers have come to expect — they will need new tools and strategies to stay ahead of the competition.
However, not every automation solution is created equal. For many businesses, only particular technology will provide the most significant return on investment.
These are some of the current popular solutions for packaging line automation and key considerations that help businesses get the most out of them. Implementing them is a guaranteed way to save money and boost efficiency while growing the bottom line.
Key Benefits of Packaging Automation
Using automation to supplement manual work in the packaging line can significantly increase the number of boxes it produces. Some systems can enable third-party logistics providers to create as many as 1,000 customized packages per hour for single and multi-line orders. These arrangements can significantly reduce pressure on human workers and allow a company to manage sudden spikes or shifts in demand more effectively.
This can provide an essential competitive advantage, especially as the e-commerce sector grows and consumer expectations continue to rise.
"With the rapid growth of ecommerce and a tight labor market, the right packaging automation system can have a big impact on your business." -Emily Newton @ReadRevmag #Packaging #Distribution Share on XOptions for Packaging Line Automation
Businesses that manage packaging in-house and third-party logistics providers both have the option to adopt full-stack packaging automation solutions. They can also incorporate solutions that automate individual packaging tasks — like void filling, pallet wrapping and labeling.
The best automation solution for a company will likely be determined by the business’s customer base or the companies a particular 3PL serves.
A common approach is to adopt an automated packaging machine with programmable tools like custom-box sizing systems that can scan items to determine the ideal dimensions. These systems can minimize or eliminate void fillers, as the box will be close to the best possible size for the item being shipped.
Eliminating void fillers can come with some additional benefits, as well — less plastic, waste and weight. Businesses concerned with their environmental impact will find that reducing the use of reduces their waste.
The system can also use information from the scanner to automate other important packaging tasks, like box labeling. However, this sort of automation system will work best in particular conditions. Logistics providers that handle parcel delivery for B2C businesses, produce more than 5,000 orders per day and primarily fulfill single-line orders can benefit most from this type of solution.
The closer a logistics provider’s situation is to this ideal, the more cost-effective this packaging automation solution will be.
Limited Automation Solutions
Other businesses may benefit from smaller-scale automation that manages only a single task or individual step in the packaging process. Because human labor is typically the largest expense in a packaging operation, identifying high-cost manual tasks that can be automated is often the first step in determining which solutions will provide the greatest return on investment.
"The right packaging automation solution is highly dependent on the product type and volume, the human labor involved, and type of customer served." -Emily Newton @ReadRevMag #Packaging #Warehousing Share on XEliminating these tasks that require a significant amount of dedicated human labor, or streamlining them to reduce the number of workers they need, will help a business effectively reduce operational costs.
On-demand void filling machines can significantly improve the efficiency of manual operations. Tabletop strapping machines can simplify the strapping of boxes. Simpler and smaller tools can provide similar, if reduced, benefits without requiring the same initial capital investment.
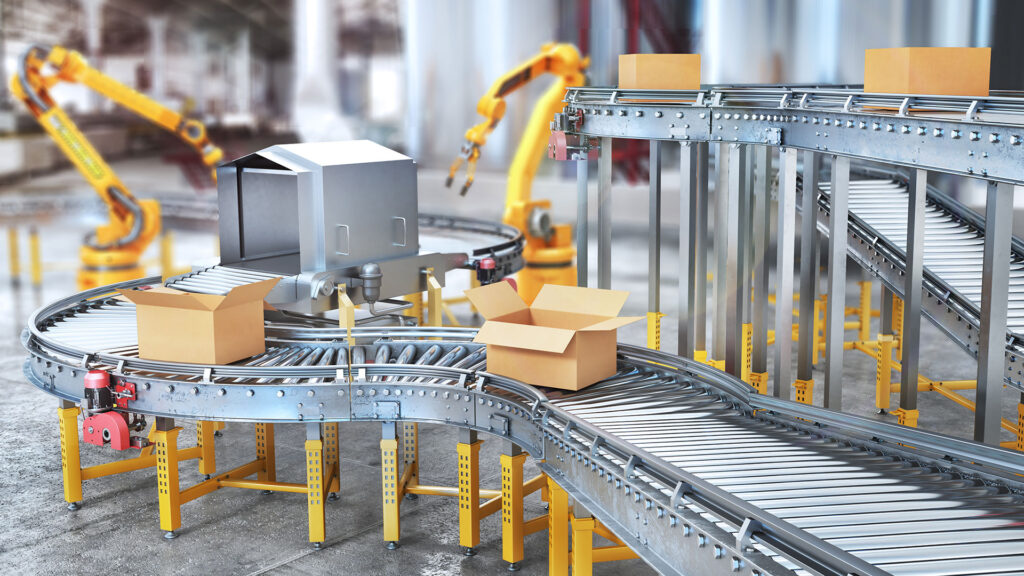
Essential Considerations for Integrating Packaging Automation
The cost-effectiveness of a new system will be determined primarily by how good it is at solving costly business problems. For example, an automated pallet wrapper will minimize or eliminate the labor costs associated with wrapping and potentially improve facility throughput. These machines can reduce production bottlenecks and reduce labor costs in facilities that produce a large number of packages needing to be pallet wrapped.
Other essential considerations include the cost and quality of the system being adopted. The quality and effectiveness of one part of your automation solution can also have major implications on the rest of a business’s packaging equipment. Machines that produce poor seals, whether they’re uneven, weak or damaged, can be more difficult to cut. Over time, this can damage bagging knives and other key items. This can significantly reduce the cost-effectiveness of a solution by increasing maintenance and operational expenses.
Effective system integration is also key. The new automation solution should integrate with the machines in a packaging facility and integrate with business systems. For example, sensors and diagnostics can be passed up to high-level networks that allow tracking of company-wide maintenance information. Data from a digital supply chain network, an ERP or CMS can also be passed down to individual facility machines.
Timing the implementation of packaging automation will also improve the cost-effectiveness of a new system. Businesses nearing maximum capacity and expecting to grow often benefit from a new packaging automation solution. A logistics provider that has struggled with bottlenecks may also see improvements.
However, downtime that can come with the integration of a new system may also reduce cost-effectiveness. For example, adapting to a new solution during the holiday season could be much more costly than integrating the same fix when business is slow.
Using Automation to Reduce Operational Costs and Improve Packaging Efficiency
Cost-effective automation can help any retailer or logistics provider streamline operations and better handle current market conditions. Typically, businesses benefit most from the solutions that will help them eliminate bottlenecks and reduce labor costs.
Solutions that manage the entire packaging process or handle a single task may be helpful, depending on the business’s size, packaging demands and the disruption a new solution may cause.
In any case, effective integration of a new automated tool or solution will be necessary for companies that want to see success. Best practices will help a business integrate new methods with other facility machinery and company-wide systems, which will streamline operations and save money. All told, automated packaging can have a major and beneficial impact on business, and forward-thinking facilities looking for a competitive advantage should seriously consider implementing this technology.
Recommended Posts
- Are Micro Fulfillment Centers the Next Frontier in Retail Logistics?
- Rethinking Defense Supply Chains with Network-Based Command Centers
- How to Use Predictive Analytics to Streamline Cross-Border Logistics
- AI Plus Humans for Resilient Freight Forwarding in a Complex World
- Modern Defense Supply Chains: The Essential Capabilities for Multi-Domain Operations
- 6 Ways Technology Makes the Supply Chain More Efficient - October 25, 2023
- How Digitization is Enhancing Supplier Relationship Management - May 9, 2023
- A Guide to choosing the Best Pallet Wrapping For Your Needs - November 28, 2022