This post has already been read 30587 times!
As first-generation ERP approaches end-of-life, companies can spare implementation nightmares and capability shortfalls by adopting a new strategy
Imagine this…
You’re a leading European retailer expanding worldwide. You’ve invested $557 million implementing a new inventory management system from one of the world’s leading enterprise tech companies. You dedicate roughly a thousand of your staff and a few hundred consultants to a project that is expected to have a major impact on the business. And it does.
The project burns up $557 million, seven years of resources and grueling effort… then dies.
A $557 million Halloween horror story... unfortunately for one unlucky retailer, it's true. Share on XThis is what Lidl had to endure, after a seven-year ERP implementation, riddled with problems, failed to deliver expected results. Computer Weekly reported:
“…Lidl said the legacy system was hampered by process breaks, redundant master data storage, integration gaps and functional restrictions. Multiple interfaces and modules and a decentralised server structure made the task of running and maintaining the system increasingly complex.”
Executives told staff that the strategic goals defined by the project could not be achieved within the current project and budget constraints. “We are practically starting from scratch,” a company insider told Handelsblatt.
“It is gambling. You have 50-50 chance that the CEO will get the right outcome.”
– Derek Prior, former Gartner analyst with ResultingIT
ERP disasters and disappointments are well documented. According to one study, the chances of success with one major ERP vendor were only 50-50. Only 36% of respondents believed their project kept to the original plan, and 48% said the project failed to achieve its business objectives.
ERP implementations are high risk, and often fail to deliver the intended business value. One leading system was considered a failure in 48% of the implementations. Share on XWhile things seem to have improved in recent years, the long history of epic failures points to a fundamental weakness. There are all kinds of excuses for the failure of ERP projects, but the question is: why is ERP so uniquely prone to failure? Implementations fail at a high rate, and when they don’t fail outright, they often fail to deliver the expected functionality and value for the investment.
“In 1998, the U.S. Navy embarked on a set of four enterprise resource planning (ERP) pilot projects focused on SAP software. However, by 2005, the effort was scrapped, costing the Navy $1 billion… [T]he failure affected 90,000 Navy employees globally, who struggled to gain efficiencies from these ill-fated systems.”
Bill Baumann, Panorama Consulting
I won’t cover it here, as the problems with ERP have been well documented and stem from its enterprise-centric roots back in the Cold War era. The tragic side of this horror story is that no company should have to endure years-long implementations, cost overruns, subpar functionality, and poor results that fail to support the organizations strategy.
Today there is a better way.
Digital Supply Chain Networks
A lot has changed since the origins of ERP. Today, the business landscape is very different with supply chains spanning the globe and trading partners needing to communicate and collaborate much more closely. Rather than connecting siloed ERP and legacy systems together, supply chain partners can connect to a single cloud network, share data and work together to run their businesses in real time.
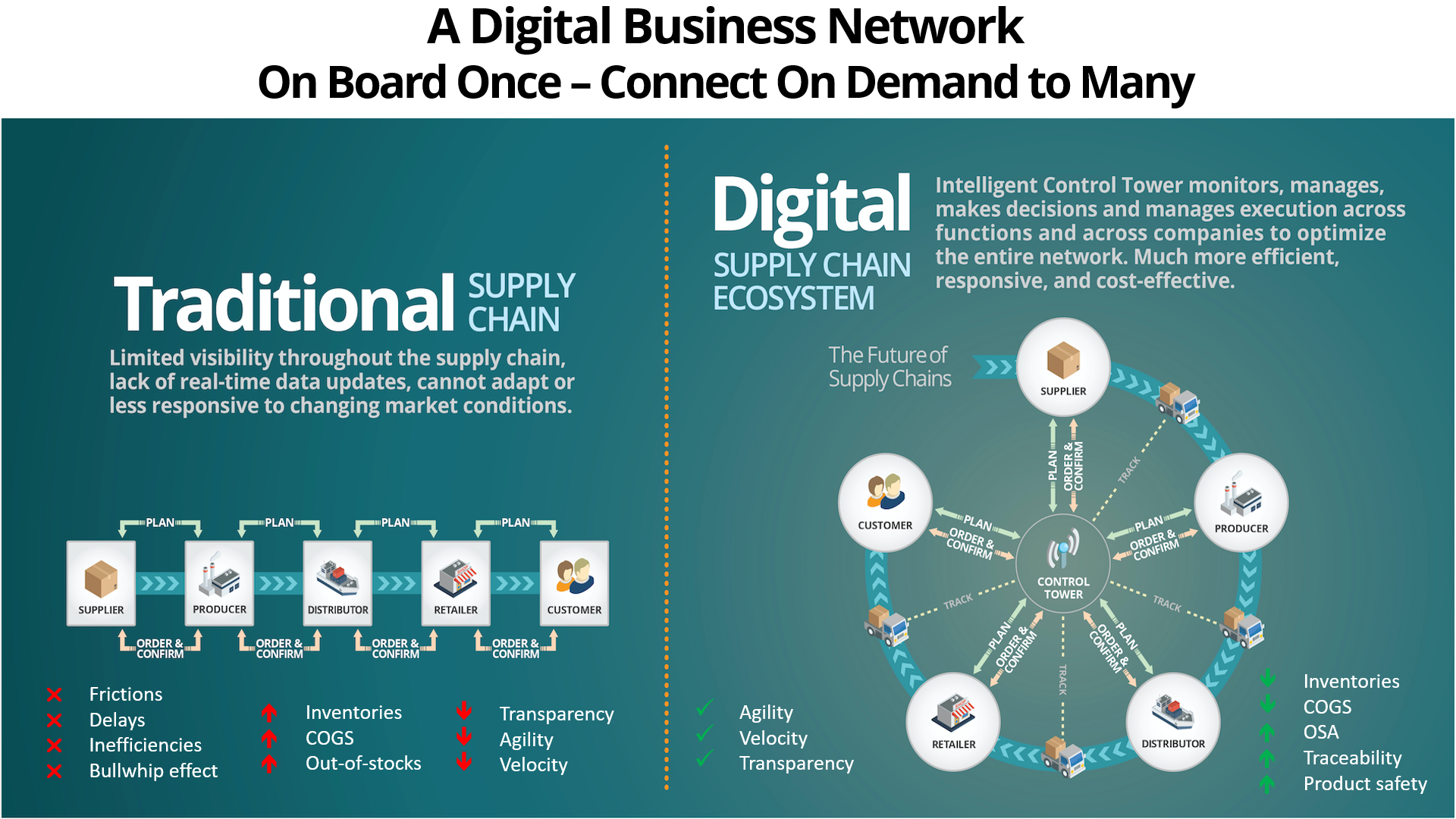
They can leverage high volume, high resolution data, to monitor their businesses and supply chains across the globe. Rather than point-to-point connections between systems and trading partners, all supply chain partners connect once to the network which maintains a real-time single version of the truth. Changes and updates are propagated in real time to all relevant parties (filtered by a permissions framework).
Partners are able to not just see status updates and alerts, but to take action and collaborate; for instance, create and promise orders or tender and accept shipments. And with the help of intelligent agents and generative AI, be alerted to, and respond to issues almost instantaneously as they occur.
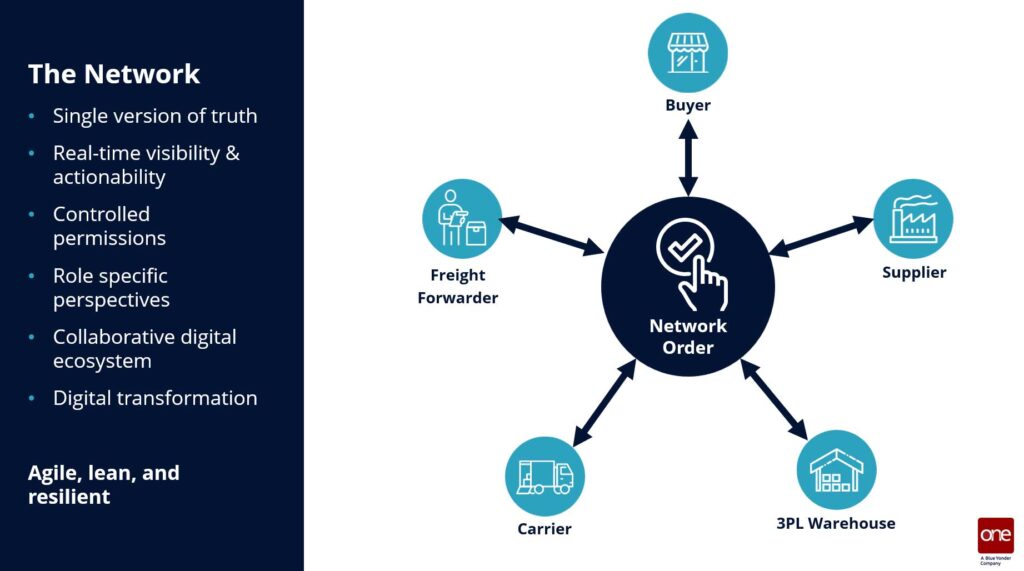
This is the new supply chain model of real-time, multi-party and multi-tier supply chain networks. Chainlink Research has covered the architecture of this new model extensively in their report, Supply Chain Networks Revealed.
ERP is Not Dead, It Plays a New Role
Neither do companies need to dispose of their ERP and legacy systems, which provide significant value in the right role. These systems provide invaluable capabilities in finance and human resources, where they excel, and where sharing data with partners is not a priority.
But many of these legacy systems house data and functionality that can play an important role in the supply chain, including systems such as ERP, WMS, TMS, MRP. With an advanced digital supply chain networks, companies can connect these systems and leverage this data on the network, by sharing it across their trading partners.
A single connection to the network enables this data to break out of the silo and be shared with any number of relevant partners. The network can even orchestrate multi-party workflows that span partners and systems, delegating some flows (or steps in a flow) to legacy systems.
Less Shocking…
This Dual Platform Strategy – one for Network Business Operations and one for Enterprise Finance – means no data gets lost and no IT investment is wasted. It enables businesses to leverage new technologies, such as artificial intelligence, internet of things, and others that are embedded in and connected to the Network.
The Network serves as a minimally disruptive “on-ramp” to a journey to supply chain transformation, delivering rapid value with minimal risk, as existing systems and processes continue to operate as normal. These systems can be switched off as the Network assumes more of the functionality, to create a (relatively) seamless transition to running the entire supply chain on a real-time digital network.
All in all, it’s a lot less scary than the typical “big bang” implementation.
Recommended: ERP versus Intelligent Business Network Platforms
What’s New
- How to Avoid a Technology Horror Story - October 31, 2024
- How Chain of Custody Strengthens the Supply Chain - October 11, 2022
- Inside Next Generation Supply Chains - November 8, 2021