This post has already been read 25533 times!
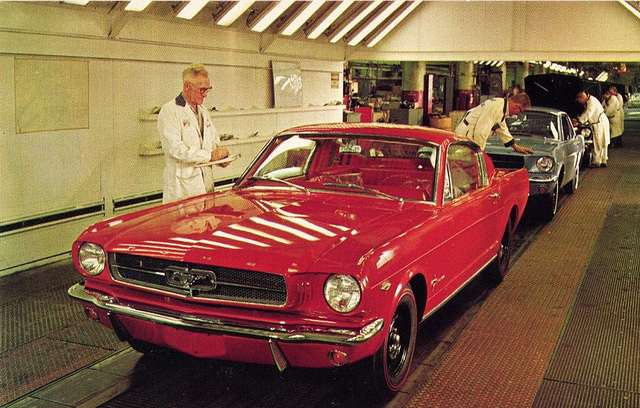
This is an ongoing series of posts on new developments within the automobile supply chain, with examples of best practices. In my last post, I talked about why a network model makes so much sense.
Today I want to explore how automobile suppliers are improving their operations via inventory replenishment policies.
Effective inventory replenishment policies in use today include the 830/862 converted to a delivery release, KanBan, Min/Max, and Sequencing. Spot buys may be used as well during product launch or pre-production.
Improved technologies now provide the ability to optimize truckloads simultaneously with inventory using pull policies.
Using the 830/862 basically constitutes a push schedule from the supplier into their customer’s manufacturing operation. Truckload optimization is simpler under this technique, but a price is paid in excess and obsolete inventory. Improved technologies now provide the ability to optimize truckloads simultaneously with inventory using pull policies. In fact under today’s prevailing strategies around Lean, many companies are implementing technologies that will allow them to move from push to pull. Major automotive Subsystem and Tier 1 Suppliers are actually including statements to this effect in their 10k filings.
KanBan, being one of the simplest pull policies, is designed to pull supply based on a rate of consumption. The KanBan binning technique is designed to provide discrete quantities the supplier must monitor and use to calculate required shipment quantities.
Min/Max, a more flexible pull policy, provides a range of acceptable inventory levels the supplier must monitor and use to calculate their required shipment quantities. Supply is done dynamically based on a consumption rate, and therefore additional consideration can be made for transportation optimization under this policy.
And finally Sequencing is designed as an hourly or shift based replenishment technique where data is sent to suppliers to prioritize shipments. This method is commonly used when suppliers make multiple deliveries in the same day to a given site.
Using these types of standardized inventory replenishment policies allows customers to reduce supply chain variability, optimize inventory levels and minimize freight expense. Typical measurements include inventory turns, truck utilization, and premium freight reduction. Unfortunately in order to provide this type of functionality most ERP vendors must use plug-ins that are not integrated as part of the transactional flow.
Unfortunately in order to provide this type of functionality most ERP vendors must use plug-ins that are not integrated as part of the transactional flow.
However when these types of replenishment policies are included as part of an overall supply network initiative, the customer will also enjoy full internal & external visibility of component parts based on a technology platform which supports both an automated and an interactive capability to enable full electronic commerce, including the ability to communicate replenishment signals across the global supply network in real time.
A complicating factor for a Tier 1 supplier will be that under this multi-policy replenishment environment, it is possible that the Tier 2 suppliers serving a particular customer could receive replenishment signals being driven by different replenishment policies across various receiving plants, or a single plant could be using multiple replenishment policies across a varied group of suppliers. In a traditional point to point policy and communication architecture this would be a difficult scenario to manage. In the type of subscription based network environment we have been discussing it actually becomes quite simple, especially given that technology is now available to handle all the heavy lifting.
Although many factors are considered when choosing proper replenishment policies, primary consideration is typically given to the specific lean manufacturing strategy being deployed, the variability of customer demand, and the overall logistics footprint in terms of delivery lead times.
To determine the optimal replenishment method to use for each component, manufacturers have traditionally adjusted on an annual basis or when operational or supply chain conditions shift (i.e. when a supplier moves production to another location that is geographically different than the existing supplier location).
A better method would be to use recent and historical performance and outcomes to adjust replenishment policies in order to improve performance. Using the power of an advance network platform, it is possible to select from an improved set of policies, while also implementing automated exception handling at increasing levels of precision. In addition inventory planning can be invoked which helps establish target inventory levels within the policies based on variations and lead times.
Automotive Inbound Supply Best Practices
If you’d like to know more on this and related subjects, I recommend you read the new Automotive Inbound Supply Best Practices whitepaper. It’s an incredibly comprehensive deep dive of what automotive suppliers are being asked to do, and it provides a clear road map for how they can achieve it. I think you’ll find it enlightening and useful as a practical guide to improving your business.
- Generative AI: Force Multiplier for Autonomous Supply Chain Management - May 23, 2024
- Top 5 Signs Your Supply Chain is Dysfunctional - August 19, 2022
- Why a Network Model Makes Sense for Automotive Suppliers - July 30, 2019